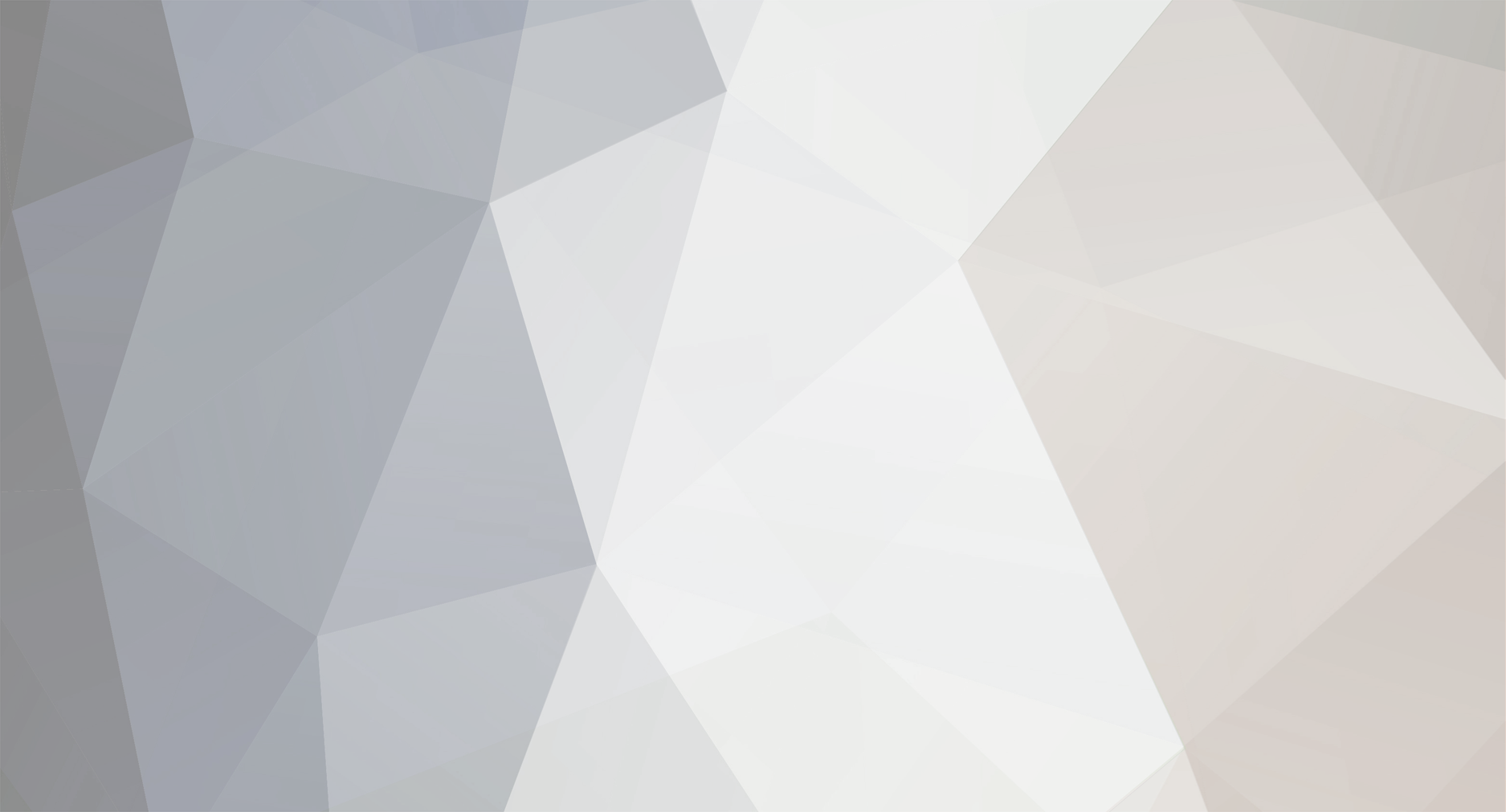
Tyler2012
New Member-
Posts
4 -
Joined
-
Last visited
Content Type
Profiles
Forums
Calendar
Everything posted by Tyler2012
-
Fury 325 Support Failure
Tyler2012 replied to Oldschool75's topic in Other Amusement Parks & Industry News
Why would the park reach out to him? -
Fury 325 Support Failure
Tyler2012 replied to Oldschool75's topic in Other Amusement Parks & Industry News
I'm not sure I understand the reference to post-tensioned concrete, but if I'm reading the rest of this correctly, I think you're saying there isn't much load in the diagonal member when there isn't a train running on that portion of the track? If so, I agree. The tension load is caused by the dynamic forces of the train moving along the track, and the diagonal member probably doesn't have much to do when the coaster isn't operating. That being said, from an engineering perspective, that member is very clearly a tension member. That isn't to say it is not also loaded in compression at some point, but I'd be willing to guess the largest force it sees by far is a tensile one. This may not be immediately apparent to the public (there's no reason it would be), but I think most people could understand why with a quick 5-minute lesson. The diagonal member will be loaded in tension when the train passes just by virtue of the support and track configuration. As shown in the video where the train rides over the failed support, the top-most portion of the support moves to the right since it is no longer attached to the rest of the support. If not for the separation, the diagonal member would resist that rightward movement by pulling the vertical member back into place like a rope or chain, therefore the diagonal member is in tension in that situation. The vertical member, however, is likely modeled as a compression (i.e., pushing) and/or flexural (i.e., bending) member, though. The diagonal member goes into tension when loaded by the train, but tension doesn't have to be put into the support during construction. Referring to your first paragraph, post-tensioning strands (and prestressing strands, for that matter), are installed in concrete for the sake of the concrete, not the steel. Steel does not have to be prestressed or post-tensioned to effectively carry load (most of the time...nor does traditionally reinforced concrete that uses only rebar). The sand just adds extra dead load the diagonal member has to deal with when there is no train- it wouldn't have much of an effect on the member's tensile capacity. But steel, whether a box, tube, angle, wide flange (i.e., an I-shaped beam or column), strand, wire, or cable, can be put into tension by any pulling force applied to the member. The shape doesn't matter as long as the member can be pulled. I have no idea how often B&M expects the entire structure to be inspected, but I would be very surprised if it's the "daily" inspection some folks are saying "should" happen. We'll see if I figured out how to use the quote feature with interspersed comments. My apologies if not. -
Fury 325 Support Failure
Tyler2012 replied to Oldschool75's topic in Other Amusement Parks & Industry News
Thanks! I can't say the support was properly designed (or that it wasn't for that matter, even with the failure), but your summary is basically correct. The diagonal member would be loaded primarily in tension/pulling. I wouldn't say steel works "best" in tension, though, just that if a designer has the option of resisting a load with a tension or compression member, the tension member will likely be more efficient (but that doesn't mean better). I could speculate what may have happened, but it would only be a random guess that could be right, or very, very wrong. Design defects, construction defects (e.g., weld installation issues, foundation settlement), material defects (i.e., weld material and/or base metal (i.e., the steel being welded together)), failure due to residual stresses (i.e., stresses left over from manufacturing the steel and/or welding it together), or all these in some combination could have contributed to the failure. But yes, a metallurgist will almost certainly be hired to look at the weld(s?) there. Steel absolutely behaves in a more brittle manner at lower temperatures (meaning it tends to crack instead of stretch the colder it gets), but I doubt that contributed much to the failure. It certainly could have, but even if Carowinds operates the ride year-round (and I don't know if they do or not), I don't think the temperatures are so low that special considerations would be needed in this situation. I didn't deal with dynamic structures though (i.e., structures where loads are applied quickly), so I could be way off base. -
Fury 325 Support Failure
Tyler2012 replied to Oldschool75's topic in Other Amusement Parks & Industry News
Structural (though non-roller coaster) engineer here. There are many factors that dictate support placement. For instance, existing structures and/or other interferences above ground (like TR:TR’s entrance cave as shown in the picture of Diamondback that was posted earlier), soil conditions underground that determine where footings can go, structural efficiency, aesthetics, etc. Assuming soil conditions are generally uniform in this area of Fury 325 (which may or may not be the case), it appears the only other condition that would determine where footings could be constructed is the location of the parking lot. Supports in this area may have been designed to avoid being built in the parking lot, but structural efficiency may have also played a role. Let me explain: steel members in tension (i.e., pulling) are generally more efficient (i.e., less material is needed to resist the same force) than steel members in compression (i.e., pushing). Think of a rope: you can pull a truck with it, but if you “push“ on a rope, it just crumples; it can’t resist compressive forces at all. The structural engineering equivalent of “crumpling” (more or less) is buckling, or the sudden lateral (i.e. sideways) deflection (i.e., movement or displacement) of a supporting member. Think of a piece of uncooked spaghetti: if you push on the ends, the spaghetti bends, or buckles. The diagonal portion of the Fury 325 support that failed would have been loaded primarily in tension by the passing train, therefore it could be smaller than if it were loaded in compression (in which case the diagonal support would have been placed on opposite side of the vertical support). In this particular situation, using a tension brace or a compression brace isn’t right or wrong. It just depends on several other factors, and I imagine one of them was efficiency. Also, as I posted on another site, unless you have access to B&M’s inspection requirements for Fury 325, and proof those requirements were not met, blaming maintenance for this incident is ignorant and irresponsible. That a structural failure like this occurred is not an automatic indication that maintenance was not being done properly. Design, construction, and/or material issues could have contributed to this just as much as anything else. Until (if) a report detailing the cause of the failure is released, no one without detailed knowledge of the ride and its operations should be blaming anyone. Statements regarding what the park or maintenance “should” have been doing are likely uninformed. Engineers can roughly determine how many cycles (i.e., when a structure is loaded and unloaded, or stressed and unstressed) a steel structure can withstand, which can be used to determine how often a component should be inspected. Keep in mind, most of the bridges in the US have arm’s length inspections only every 12 to 24 months. I don’t see why the structure of a steel roller coaster would be much different.